
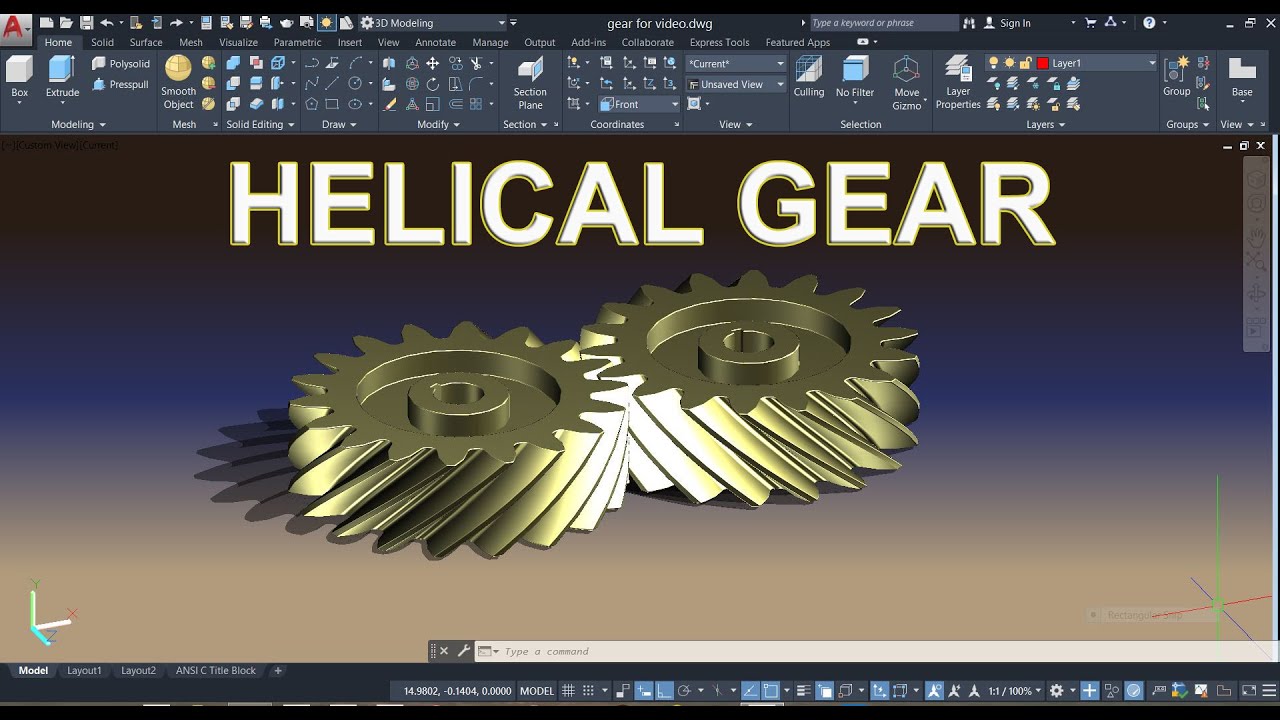
Deb K, Agrawal RB (1994) Simulated binary crossover for continuous search space.Colbourne J (1987) The geometry of involute gears.Chen Z, Zhai W, Shao Y, Wang K (2016) Mesh stiffness evaluation of an internal spur gear pair with tooth profile shift.Association AGM (1994) Fundamental rating factors and calculation methods for involute spur and helical gear teeth.Abderazek H, Ferhat D, Ivana A (2017) Adaptive mixed differential evolution algorithm for bi-objective tooth profile spur gear optimization.Abderazek H, Ferhat D, Atanasovska I, Boualem K (2015) A differential evolution algorithm for tooth profile optimization with respect to balancing specific sliding coefficients of involute cylindrical spur and helical gears.The developed stress in the helical gear pair is found to be well within the allowable stress limits for the gear pair. These CAD models are used for performing finite element analysis (FEA) on the helical gear set for analyzing the stress developed in the gear pair. 3D computer-aided design (CAD) models have been developed by using the optimized results obtained from RCGA and commercially used software. The optimal design solutions obtained with and without profile shift are recorded and compared with commercially used software for validation. Specific sliding, transverse contact ratio and face width constraint along with other strength requirements are the design constraints. Profile shift coefficients for gear and pinion have been included as design variables along with mostly used generic design variables, module, face width and number of teeth on pinion. Real-coded genetic algorithm (RCGA) has been used to attain minimum volume of helical gear pair. Preventing undercutting, balancing of wear and bending fatigue strength and centre distance adjustment are some of the advantages of profile tooth modifications.

Effect of profile shift and specific sliding on design optimization of helical gear pair have been studied and found to be beneficial of great importance. Optimized modification in tooth profile has immense benefits in gear operations. Specific sliding needs to be balanced for enhancing wear and scuffing resistance of helical gears.

Your focus can be on the design at hand and not on the navigating routine.A unique perspective in design optimization of helical gear pair has been emerged and presented in this article. Your learning curve in using the software is faster than any other package on the market due to the widespread use of Excel. Web Gear's Software uses the power of Microsoft Excel to perform all necessary design calculations.
